Journey to World-Class Safety
Emera’s commitment to safety and health is a critical part of how we work. Our business is on a path to achieve world-class safety, and we make progress by deepening our culture of safety and health, and strengthening our disciplined approach to safety performance.
We think about safety as a journey, because we recognize that even as we improve our safety record over time, we have more work to do. This is especially true following serious and challenging safety incidents. When faced with such incidents, we’ve moved quickly to take action - to understand what went wrong, and to adapt and strengthen our safety approach - so we can avoid future harm. We have to do better, and we’re committed to doing what it takes to ensure that everyone at Emera lives and works injury-free.
Responding to Incidents
We are saddened that in 2016 there was a team member fatality at Grand Bahama Power. In 2017, there was another team member fatality in connection with the Maritime Link. Additionally, a workplace accident involving a team at Tampa Electric in 2017 resulted in five deaths and one person critically injured. Each of these incidents is different, but in all cases we have taken immediate steps to ensure team safety, and conducted thorough investigations working with the appropriate experts and authorities to uncover root causes and ways we can avoid future harm. These events are tragic and, while not typical of our strong safety record, they strengthen our team’s commitment and resolve to work and live safely. We must do better.
Common Commitment
Emera companies share a strong commitment to occupational health and safety. As we work to achieve world-class safety in all our companies, our teams have detailed safety programs including objectives, measures, reporting, training and tracking systems – informed by international best practices like OHSAS18001. We continually revisit our safe work practices and, through programs like Safe Start and Safety by Design, we ensure that all of our team members and work partners understand the importance of being properly prepared and protected, and eliminating hazards.
Culture of Safety
At the beginning of shifts and meetings, team members take a moment for safety, sharing information on the best safety practices and lessons learned from our operations. Our companies hold regular safety stand-downs to talk about current areas of safety focus. Team members are encouraged to set safety-related personal development goals, and take part in the many safety training sessions offered throughout the year. And we take time during annual events, like the National Day of Mourning and North American Occupational Safety and Health Week, to be mindful of the importance of safety in our business.
Focus on Preventative Safety
Emera is increasingly focused on leading safety indicators, which means the things our team members can do that help prevent safety incidents from happening in the first place. In 2016 we increased the number of safety-focused site visits by our leaders, improved our focus on safe work observation practices and encouraged all our teams to take part in near-miss and proactive reporting. Through measures such as these, we continue to reinforce our preventative approach to safety.
Safety & Performance
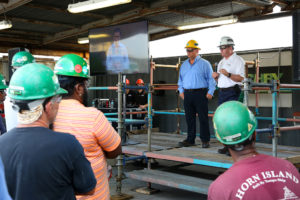
We back up our commitment to safety by linking it to company performance. Each year, we set safety-related targets and goals in our Balanced Scorecards, which determine annual performance pay. Helping us establish, achieve and monitor those goals are our network of safety professionals, who work collaboratively across companies to develop a common approach to procedures, reporting, training and tracking. Emera’s safety professionals meet in person at our annual Safety Summit, a forum to set shared priorities and uncover new approaches.
Employee Safety Team at Emera Maine
Team members at Emera Maine show their commitment to safety by stepping up and taking part in the Employee Safety Team. Participants take on responsibility for championing and improving various aspects of safety in and around the workplace, including annual safety planning, public safety, tooling, office safety, fleet safety, training days and incident reviews. The efforts of this employee-led team augment the work of the formal safety program at Emera Maine.
Athletic approach
In January 2017, Peoples Gas piloted an innovative ergonomic program focused on fundamental movements to address sprain/strain injuries common to our industry. It’s not uncommon for the Peoples Gas team to have one or two of these injuries every year. In fact, over the past 10 years, approximately 50 per cent of injuries involved sprain/strain. Similarly, Tampa Electric has partnered with the University of South Florida’s Sports Medicine & Athletic Related Trauma Institute to find new ways to help linemen minimize and eliminate athlete-like injuries. Best practices from that partnership can be witnessed at the company’s Skills Training Center’s interactive training yard. Emera Maine, with a similar focus on ergonomic injury prevention, has engaged with local occupational health experts in an Industrial Athletics program and individualized injury rehabilitation at work programs.
Achieving Safety Milestones
We take safety seriously, and we believe it’s important to recognize when members of our team demonstrate excellence in safety. That was the case for Emera Energy’s Bayside Power team in 2016 who achieved 6,000 days without experiencing a lost-time incident – which means no serious safety incident since the plant began operations. That milestone was repeated soon after in 2017 by two other Emera Energy teams: Tiverton Power and Rumford Power. The team at Nova Scotia Power’s Tufts Cove generation plant also achieved a major safety milestone in 2017, reaching 4,745 days without a serious safety incident.
Emera Lost Time Frequency Rate (LTF)
Notes: Per 200,000 hours worked LTF rates for TECO Energy have been added retroactivity to allow for a more accurate comparison of performance.
Emera All Injury Frequency Rate (AIF)
Notes: Per 200,000 hours worked AIF rates for TECO Energy have been added retroactivity to allow for a more accurate comparison of performance.
Dominica Electricity Services launches Health, Safety and Environment Month
The Dominica Electricity Services team achieved a safety record in 2016, recording the lowest-ever injury frequency rate in the history of the company. To continue to build on this momentum, the team recently launched an annual Health, Safety and Environment Month that will help to deepen team member commitment and bring wider community attention to the importance of safety. Dominica Electricity Services is targeting zero workplace injuries by 2020.
Dominica's Electricity Services team recorded the
lowest-ever
injury frequency rate in the history of the company in 2016
Safety Planning at New Mexico Gas
New Mexico Gas is a relative newcomer to the Emera companies, but the team in New Mexico share in the commitment of our business to attain world-class safety. In 2016, the New Mexico Gas team made significant progress on developing a new five-year safety plan which includes a focus on safety leadership, team member engagement and reducing the rate of safety incidents. This kind of plan is an important tool that Emera companies use to ensure our business-wide safety approach is being put in place everywhere we work.